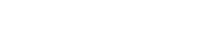
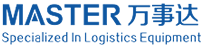
Recently, the automated vertical warehouse project undertaken by MASTER officially started.
The project is located in the southeast of Jiangsu Province. It adopts an automated three-dimensional storage method and an intelligent management system, integrating automatic warehousing, intelligent storage management and automated outbound delivery.
Project background
Warehouse size: internal 79.6*27.9 meters
Warehouse height: zero surface net height 21 meters
Storage requirements: 4,800
Process: automatic warehousing.
Project difficulties
The warehouse is a newly built warehouse. During the overall construction process, the demolition and reconstruction process was reduced. Traditional cargo storage has many disadvantages:
Spatial layout: Traditional warehousing often lacks systematic space planning in the initial planning, and the space utilization rate is low.
Operation efficiency: It is highly dependent on manual operation and cannot meet high traffic requirements. There is a lack of refined process design in each link.
Flexible logistics: The site space is compact and does not support secondary transformation of the site environment.
Solution
Selected products: 3 double-deep stackers, 1 elevator, 18 chain conveyor lines, 22 conveyor line corresponding control systems, and related supporting hardware equipment.
System configuration: WMS warehouse management system, intelligent and automated software and hardware processes
Project value
Storage capacity increased by 4.5 times
In and out of storage efficiency improved, 24/48 trailers per hour.
Reduce unnecessary labor costs
All-round safety guarantee
MASTER strives to promote new automated and intelligent storage models.
Recently, the automated vertical warehouse project undertaken by MASTER officially started.
The project is located in the southeast of Jiangsu Province. It adopts an automated three-dimensional storage method and an intelligent management system, integrating automatic warehousing, intelligent storage management and automated outbound delivery.
Project background
Warehouse size: internal 79.6*27.9 meters
Warehouse height: zero surface net height 21 meters
Storage requirements: 4,800
Process: automatic warehousing.
Project difficulties
The warehouse is a newly built warehouse. During the overall construction process, the demolition and reconstruction process was reduced. Traditional cargo storage has many disadvantages:
Spatial layout: Traditional warehousing often lacks systematic space planning in the initial planning, and the space utilization rate is low.
Operation efficiency: It is highly dependent on manual operation and cannot meet high traffic requirements. There is a lack of refined process design in each link.
Flexible logistics: The site space is compact and does not support secondary transformation of the site environment.
Solution
Selected products: 3 double-deep stackers, 1 elevator, 18 chain conveyor lines, 22 conveyor line corresponding control systems, and related supporting hardware equipment.
System configuration: WMS warehouse management system, intelligent and automated software and hardware processes
Project value
Storage capacity increased by 4.5 times
In and out of storage efficiency improved, 24/48 trailers per hour.
Reduce unnecessary labor costs
All-round safety guarantee
MASTER strives to promote new automated and intelligent storage models.